Maintaining high standards of quality is an absolute necessity in highly regulated industries such as pharmaceuticals, biopharmaceuticals, and medical devices. One of the essential components of a robust Quality Assurance (QA) system is a well-developed Corrective and Preventive Action (CAPA) strategy.
An effective CAPA strategy addresses immediate compliance issues and implements long-term improvements to prevent future occurrences. This blog post explains the value of an effective CAPA strategy and provides insights on how to build one.
The Importance of an Effective CAPA Strategy
A CAPA strategy is crucial for several reasons:
- Regulatory Compliance: Regulatory bodies require organizations to have CAPA procedures. Non-compliance can result in severe penalties, including fines and product recalls.
- Quality Improvement: Organizations can improve their processes by identifying root causes and implementing corrective actions, resulting in higher product quality and safety.
- Risk Management: An effective CAPA strategy helps identify and mitigate potential risks early before they escalate into significant issues.
- Customer Satisfaction: By addressing and preventing issues, companies can consistently meet customer expectations, enhancing customer trust and loyalty.
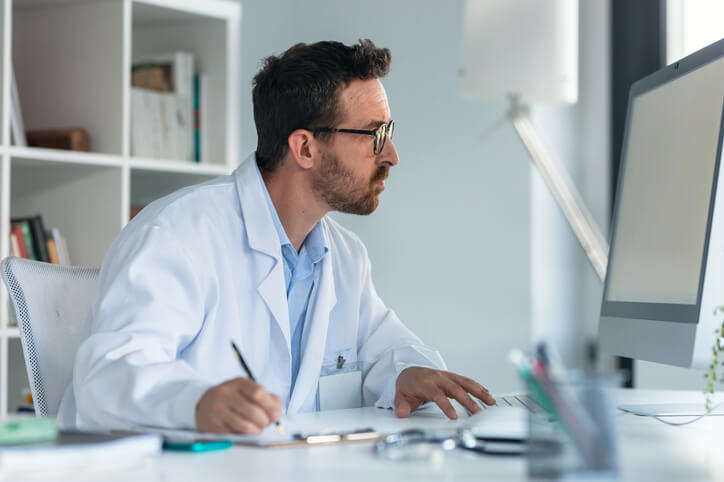
An effective CAPA strategy helps identify risks early and mitigate them.
Building an Effective CAPA Strategy
Building a robust CAPA strategy involves several key steps:
- Understanding Lean Principles: The first step in developing an effective CAPA strategy is understanding Lean principles. Lean methodologies focus on creating more value for customers with fewer resources by optimizing processes and eliminating waste. Incorporating Lean principles helps streamline the CAPA process, making it more efficient and effective.
- Good Processes Essentials (5 Principles of Lean): Ensuring good processes involves adhering to the five principles of Lean:
- Value: Define what is valuable to the customer.
- Value Stream: Map all the steps that bring a product or service to the customer, eliminating steps that do not add value.
- Flow: Ensure that the value-creating steps flow smoothly without interruptions.
- Pull: Produce only what is needed when it is needed.
- Perfection: Strive for continuous improvement in all processes.
- Identifying Non-Value-Added Activities (8 Wastes of Lean): It is critical to identify and eliminate non-value-added activities. The eight wastes of Lean include defects, overproduction, waiting, non-utilized potential, transport, inventory, motion, and extra processing. By addressing these wastes, organizations can enhance efficiency and reduce costs.
- Lean Problem-Solving Methodology: Lean problem-solving involves a structured approach to identifying and resolving issues. This includes accurately defining the problem, identifying the root cause, developing corrective actions, and confirming the results.

The first step in developing an effective CAPA strategy is understanding Lean principles.
- Effective Problem Definition: A well-defined problem is halfway to being solved. Clear, concise problem statements help focus efforts on the correct issues.
- Root Cause Identification: Understanding the root cause of a problem is essential for effective corrective action. Techniques such as the 5 Whys and Fishbone Diagram are valuable tools for root cause analysis.
- Process Mapping: Visualizing the process through mapping helps identify bottlenecks and areas for improvement. It provides a clear picture of the current state and helps design an improved future.
- Corrective Action Development: Based on the root cause analysis, develop actions that address the root cause and prevent recurrence. Actions should be specific, measurable, achievable, relevant, and time-bound (SMART).
- Confirmation of Results: Finally, it is crucial to verify that the corrective actions implemented have effectively resolved the issue and prevented its recurrence. Regular monitoring and review are necessary to ensure sustained improvement.

Throughout your pharmaceutical career, it’s crucial to verify that the issue is effectively resolved.
Developing Your CAPA Expertise: Join Our Upcoming Webinar!
Building a robust CAPA strategy requires specialized knowledge. To help you excel in this crucial area throughout your pharmaceutical career, we’re offering a webinar titled “Developing an Effective CAPA Strategy” on June 20th, 2024, from 2:00 pm to 5:00 pm EST.
This webinar covers:
- Lean principles: Leveraging Lean principles helps identify and eliminate non-value-added activities within your CAPA process.
- Root Cause Identification: Learn effective techniques for pinpointing the root causes of quality issues, going beyond the surface level of “human error.”
- Process Mapping: Master the art of process mapping to visualize your processes and identify potential areas for improvement.
- Corrective Action Development: Discover best practices for developing and implementing corrective and preventive actions that address the root cause and prevent future non-conformances.
This webinar is ideal for:
- Directors, Managers, and Supervisors in the Pharmaceutical, Biopharmaceutical, Vitamins, Herbals, Medical Devices, and allied industries.
- Associates with Quality Assurance responsibilities.
Embrace this opportunity to deepen your understanding of CAPA strategies and enhance your skills in building a robust CAPA system for your organization! Register online by June 13th, 2024, to book your spot.
Are you looking for world-class quality assurance training?
Contact AAPS for more information.